Common workplace eye hazards and how to avoid them
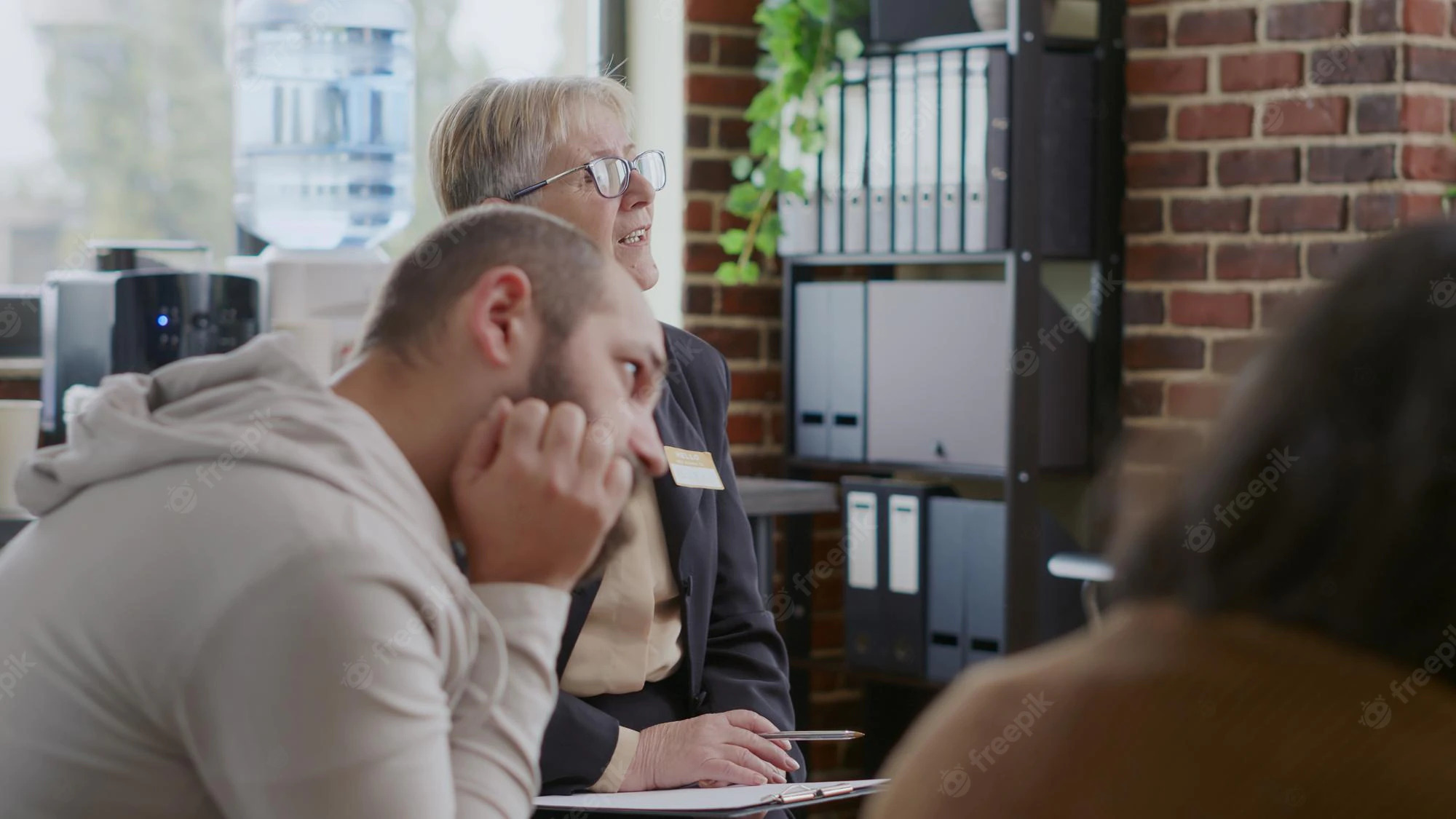
In most workplaces, when appointing new joining, instructors just give them an outline of the plan, provide the best tools, and then expect that they should start work as professionals. Indeed, without the proper education of your new and old team and suitable protective protocols is just considered in work-related injuries.
Unluckily, the number of work-related eye injuries can shock you because thousands of injuries occur daily. Therefore, one out of ten employees are missing in their workplaces because of treatment. One day missing is merely not a day without production. Other losses are medical bills, manufacturing loss, and wastage of time are some things that cannot afford in their businesses.
Common eye hazards at the workplace:
Luckily, if you become ready with small preparation, you can achieve profitable results. Let’s discuss the most common eye hazards at the workplace and how to avoid them.
- Small particles:
Small flying particles like cement, metals, wood chips and dust are a few names that are frequently worker experiences in manufacturing, construction, and some other hazardous environments. These airborne elements can hazard workers in multiple ways, whether they are falling above or blowing because of wind. When larger particles come in contact with workers, they can lead to serious eye injuries like trauma in the eye socket and eyeballs.
How to avoid?
Undoubtedly, simple safety precautions can give you different results, and you can prevent scraping and striking eye-related injuries. For new hiring, you need to ensure that there are hazard signs at your location and point out a danger of nearby danger. Besides, you should ensure that you have trained every worker with all precautions and make sure they will follow proper techniques at the work site. However, the main issue of these sites arises as these fine dust particles are a respiratory threat. Therefore, you should ensure that affected workers have proper hard hats and Prescription safety glasses (if require) every time. Besides, safety gear related to these sites is 100% certified and approved by OSHA.
- Heavy machinery and tools:
Have you ever observed, particularly on construction and manufacturing sites, there is a need for the best coordination between workers and machinery? They should come in one belt for the best results. But if they miss coordination at any point, it can create significant chaos that is highly destructive to these locations. If workers are operating a heavy machine, the turmoil can be severe.
How to avoid:
Thus, the machinery and tools need a protective mechanism, safety locks, protective switches, and the list goes on with the tools and machinery equipment. These precautions are not enough if they are not well-trained to operate them. Besides, every task should have special training that covers every step. But yet, it doesn’t mean that workers are skilled, and now they don’t need any training. Besides, you have to remind them of the best safety. Hand over them with appropriate ANSI standard safety glasses of safetyeyeglasses.com, safety gloves, and safety helmets. Safety training programs are the only way to prevent massive hazards and work-related injuries. Your workers are your asset, and you can protect them as much as possible.
- Chemical hazards:
Chemicals are comparatively more dangerous because they are invisible and significantly hazard lungs and skin before appearing in physical signs. Workers spend a substantial amount of time at workplaces, and precautions are necessary to avoid hazards. Even though there are many chemical products at home, you should take them seriously while working with them.
How to avoid?
It is hard to predict potential threats related to chemicals on a daily basis. Therefore, always stick with the safety precautions to hold them. For beginners, safety managers should ensure that with what chemicals they are working and what protections are practicing. Check them at every step while transferring chemicals in different places. Besides, there should be separate containers that store chemicals safely if they have no use.
While handling chemicals, you need to be extra careful and always keep in touch with safety managers and supervisors so they can verify the best safety. For instance, never remove safety eyewear just because they are uncomfortable. If safety glasses are not appropriate, you should consult your supervisor and discuss your problem.
Be practical
Thus, thousands of employees report medical emergencies for eye-related to their worksite every year. In a few cases, this figure can exceed. Surprisingly, 90% of eye injuries are avoidable. Thus, if you want to reduce work hazards, you need to become practical. There are plenty of ‘safety and health management program’ defined by OSHA, and you should follow them for better protection.
First, there should be a safety audit regarding eyes in the workplace to determine and remove potential threats at any cost. Besides, it is the responsibility to provide quality pairs of ANSI z87.1 prescription safety glasses and arrange safety training that should be compulsory for every worker to attend them. It doesn’t matter if your workers are temporary or professional permanent, safety training is the same for all. Try to create a healthy environment at the working site and keep safe of your workers as much as suitable.