How Do Air-Cooled Condensing Units Differ from Water-Cooled Alternatives?
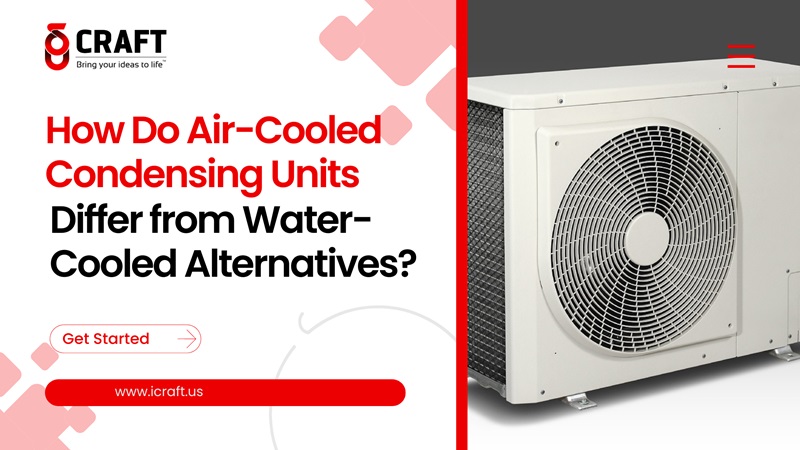
When designing industrial cooling systems, one major component decision centers on the type of condensing unit.
These motor-powered devices remove heat from refrigeration or air conditioning systems through careful compression and condensation of refrigerant vapor. Engineers can specify either air-cooled or water-cooled condensing unit types depending on several factors.
Here, we’ll clarify the performance differences between these two prevalent condensing unit designs so readers better understand their distinguishing capabilities.
1. Configurations and Operating Principles
First, what are the fundamental configurations and operation principles underlying air versus water-cooled condensing units?
Air-cooled condensing units contain a condenser made up of finned cooling coils and metal tubing carrying hot, pressurized refrigerant vapor. Large fans push outdoor ambient air over these heat exchange coils.
This enables the transfer of warmth from refrigerant inside the coils to air flowing across coil exteriors. Refrigerant thus condenses from hot gas back into cooler liquid form that can cycle back to chilling systems.
In contrast, water-cooled condensing units employ a water-fed condenser without outdoor air fans or exposed coils. The hot refrigerant flows through coiled tubing immersed in a closed-loop water reservoir instead of an open-air environment.
Chilled water gets continuously pumped through this reservoir, absorbing heat through the tube walls from the hot gas refrigerant traversing inside the coils and condensing the refrigerant. Warmer water then routes either down drains or to cooling towers for re-chilling and reuse in the condenser loop.
Those are the key operating differences between the two predominant condensing unit technologies. However several performance factors also distinguish them for various uses.
2. Efficiency and Operating Condition Considerations
From an efficiency standpoint, water-cooled condensing generally provides advantages, especially in hot or dirty locations. Water-cooled condensing units experience less intake air temperature fluctuation thanks to the water buffer.
This stabilizes operating pressures for improved refrigerant compression efficiency and condensation dynamics versus air-cooled condensers facing wide ambient air swings.
Water-cooled units also avoid reduced capacities from airborne particles accumulating on outdoor coils which must happen over months of air-cooled condenser operation. Since water units utilize isolated water loops, they bypass air filtering issues.
Water units also commonly distribute condenser heat to rooftop evaporative cooling towers. So they can leverage ambient moisture to aid heat dissipation from the water. Overall, these factors boost consistency for water-cooled systems.
However, air-cooled condensers hold advantages regarding first costs and installation. They utilize simpler straight heat exchange coils forgiving quicker installation. Facilities in temperate or dry regions may gain decent air-cooled efficacy too since drastic weather swings happen less often.
Just ensure adequate clearance for uninhibited airflow around the coils. Also, factor in long-term filter maintenance for air-cooled scenarios.
3. Sound Considerations
Noise profiles present another key differentiator. Due to large fan motors and high-velocity air pumping through their external coils, air-cooled condensing units generate significant operational noise reaching 90 dBA or more in some units.
Without solid acoustic isolation around the roof or ground mechanical area, this can disturb building occupants or neighboring structures.
In most layouts, much quieter water-cooled condensing units reside inside equipment rooms thanks to lacking external fan assemblies.
Some noise still results from water pumping apparatuses and connecting pipe routes. However, peak noise remains closer to 75 dBA — much easier to isolate with modern building materials compared to screaming air-cooled fans!
4. Maintenance Considerations
The type of condensing unit also impacts long-term maintenance requirements over months or years of continuous operation. Because they directly intake outdoor air air-cooled condensing units accumulate far more dust, dirt, and pollutants on their fins than isolated water–cooled alternatives.
Facility technicians must periodically wash down air-cooled condenser coils or even use chemical cleansers to restore heat transfer performance as particulate fouling blocks airflow pathways and insulates heat from escaping. Failure to clean air-cooled coils regularly can severely lower system efficiencies.
Beyond coil cleaning, staff must periodically lubricate and check fan motors, clean debris from air intakes, and ensure unhindered airflow zones around the unit. Refrigerant levels and system pressures should be routinely checked as well to catch conditioning leaks early.
By contrast, the closed water loop nature of water-cooled condensing unit systems prevents heavy fouling common with exposed air-cooled coil fins. Yet technicians still need to monitor water chemistry like pH, mineral levels, and biological growth which could degrade the circulating water’s heat absorption capacity over months. Condenser water pumps, valves, and supply lines also warrant preventative maintenance checks.
So neither system proves truly “maintenance free.” However, the largely self-contained water loop does isolate components better for reliable operation and efficiency than perpetually weather-exposed air-cooled condenser systems in most regions.
Facilities managers should account for maintenance workflows when selecting between these predominant condensing unit technologies during new construction or renovations. An ounce of prevention Maximizes system lifecycles!
Conclusion
While air-cooled units win on first cost advantage, water-cooled condensers edge out many installations regarding energy savings and acoustic comfort due to greater weatherization and lacking external fans. Architects and engineers select direction based on climate, budget, location, and usage parameters. No one-size-fits-all answer exists!
For expert consultation on the best commercial cooling system design integrating condensers, evaporators, compressors, and all supporting mechanicals customized for your environment, building needs, and budget, contact industrial HVAC partners like Integrated Design Solutions as Craft Group.